Hydraulic Systems in Industrial Maintenance: Enhancing Uptime and Reliability
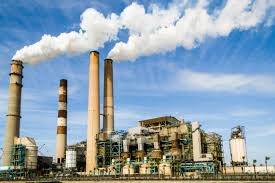
Hydraulic systems are the backbone of countless industrial operations, powering machinery with precision and control. A single failure in these systems can halt production, leading to costly downtimes and frustrated clients. Understanding how to maintain and improve the reliability of hydraulic systems is critical for any operation looking to optimize uptime and reduce inefficiencies.
Introduction to Hydraulic Systems in Industrial Machinery
Hydraulic systems use fluid power to perform heavy lifting, precise movements, or repetitive tasks. Common in industrial applications, they’re found in manufacturing, construction, aviation, mining, and shipping industries. These systems provide the strength and control necessary to operate high-pressure machinery safely and efficiently.
From cranes lifting tons of weight to assembly arms perfecting repetitive tasks, hydraulics ensure the smooth that helps businesses deliver on tight deadlines. However, despite their power, hydraulic systems demand attention and care to function at peak efficiency.
Understanding the pivotal role these systems play in factories and other demanding environments is the first step in ensuring their longevity.
The Role of Hydraulic Systems in Uptime and Reliability
Industrial success depends on two key factors—uptime and reliability. Hydraulic systems, with their precision engineering, are instrumental in achieving both.
- Uptime Advantage
Uptime, or the percentage of time a machine operates without failure, directly affects productivity. Properly operating hydraulic systems reduces unplanned downtime, allowing for consistent workflow and meeting production schedules.
- Reliability Matters
Reliability signifies a system’s ability to perform without frequent breakdowns. A stable hydraulic system ensures that industrial operations can tackle high-pressure demands without interruptions, boosting customer satisfaction and operational stability.
Businesses leveraging high-grade components like Enerpac Hydraulic Cylinders can experience enhanced performance, improved machine lifespan, and reduced operational costs.
Investing in robust hydraulic systems and proper maintenance can mean the difference between a smooth operation and costly disruptions.
Common Hydraulic System Failures and How to Prevent Them
Even the most advanced hydraulic systems are not immune to wear and tear. Knowing the common failure points can help mitigate issues before they arise.
Hydraulic System Failures
- Fluid Contamination
Contaminants like dirt, moisture, or metal particles degrade hydraulic fluid, causing inefficiencies and damage to components.
- Overheating
Excessive heat can lead to fluid breakdown and warping of system parts. Overheating decreases efficiency and can cause catastrophic system failures.
- Seal Failures
Worn-out seals are a primary cause of leaks in hydraulic systems, resulting in fluid loss and decreased pressure.
- Pump and Cylinder Wear
Hydraulic pumps and cylinders face continuous stress. Over time, wear and tear reduce their functionality.
Prevention Tips
- Replace hydraulic filters regularly to prevent contamination.
- Monitor operating temperatures and maintain cooling systems.
- Conduct regular inspections to identify worn seals and components.
- Use high-quality parts for replacements to ensure optimal performance.
Preventative care can dramatically reduce the likelihood of costly failures, ensuring maximum uptime and reliability.
Maintenance Best Practices for Hydraulic Systems
Proactive maintenance is the key to preserving your hydraulic systems. Below are the best practices every industrial operation should follow.
1. Schedule Routine Inspections
Visual and diagnostic inspections catch potential issues early, reducing the risk of failures. Check for leaks, unusual noises, and pressure inconsistencies during routine checkups.
2. Use the Correct Hydraulic Fluid
Choosing the wrong fluid or neglecting to replace it regularly can create inefficiencies and wear out parts faster. Stick to the manufacturer’s recommended type and specifications.
3. Regularly Flush the System
Flush old hydraulic fluid to remove contaminants and ensure the system operates with clean fluid.
4. Monitor Key Performance Indicators (KPIs)
Keep an eye on system pressure, temperature, and cycle times to identify unusual patterns. Modern diagnostic tools can make this process smarter and more efficient.
5. Train Your Team
Ensure team members using the machinery are trained on proper hydraulic system care. Mistakes in machine handling can lead to avoidable wear and tear.
Implementing these maintenance practices will not only protect your investment but also enhance your machinery’s efficiency.
The Future of Hydraulic Systems: Trends and Innovations
Hydraulic systems are evolving rapidly to meet industry demands for sustainability, precision, and efficiency. Here are emerging trends shaping the future of hydraulics in industrial settings.
1. Smart Hydraulics
IoT-enabled hydraulic components allow for real-time monitoring and predictive maintenance. Sensors track system health, providing early warnings for necessary repairs or part replacements.
2. Energy Efficiency
New technologies focus on minimizing energy usage. Advanced pumps, for instance, can adjust output dynamically, reducing wasted energy.
3. Compact Systems
Industries are leaning toward smaller, space-efficient designs without compromising on performance. Miniaturized hydraulic systems are now capable of delivering high power in small spaces.
4. Sustainability Focus
Environmentally friendly fluids and recyclable materials are being introduced into hydraulic manufacturing to align with modern sustainability goals.
These advancements are set to change how industries approach hydraulic systems, ensuring they remain a vital part of industrial maintenance.
Conclusion
Proactive maintenance and modern innovations are key to keeping hydraulic systems reliable and cost-effective. By preventing failures and boosting efficiency, businesses can save money and maintain a competitive edge. Start implementing best practices today to ensure smoother, trouble-free operations.