The Role of Modular Tube and Joint Systems in Lean Manufacturing Success
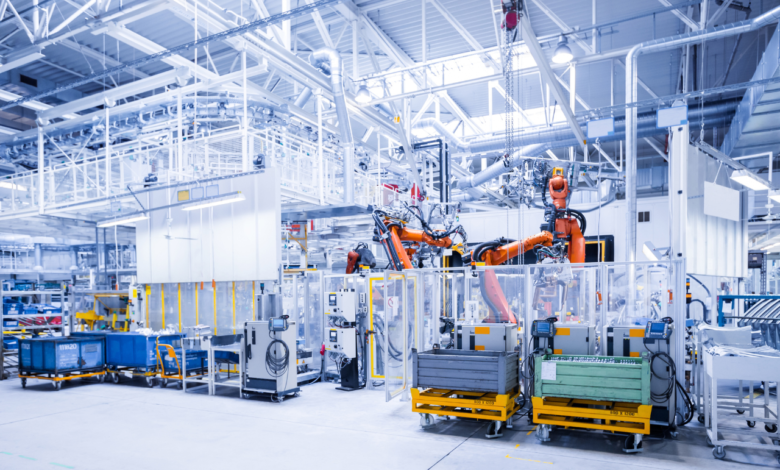
Lean manufacturing is built on the principles of efficiency, adaptability, and waste reduction—qualities that are increasingly critical in today’s fast-paced industrial landscape. A key enabler of these principles is modular tube and joint systems.
These systems offer manufacturers the ability to design, modify, and scale workstations, storage racks, and production lines without significant downtime or cost. This article explores how modular tube and joint systems contribute to lean manufacturing success and why they are becoming indispensable in modern industries.
What Are Modular Tube and Joint Systems?
Modular tube and joint systems are customizable structural frameworks made from lightweight and durable materials like aluminum or coated steel.
Key Features:
- Flexibility: Easily assembled, disassembled, and reconfigured.
- Durability: Built to withstand industrial environments.
- Customizability: Designed to meet specific workspace or production needs.
- Scalability: Expanded or reduced without major redesigns.
Example Use Cases:
- Adjustable workstations for ergonomic improvements.
- Conveyor systems for streamlined material handling.
- Customizable storage racks for inventory optimization.
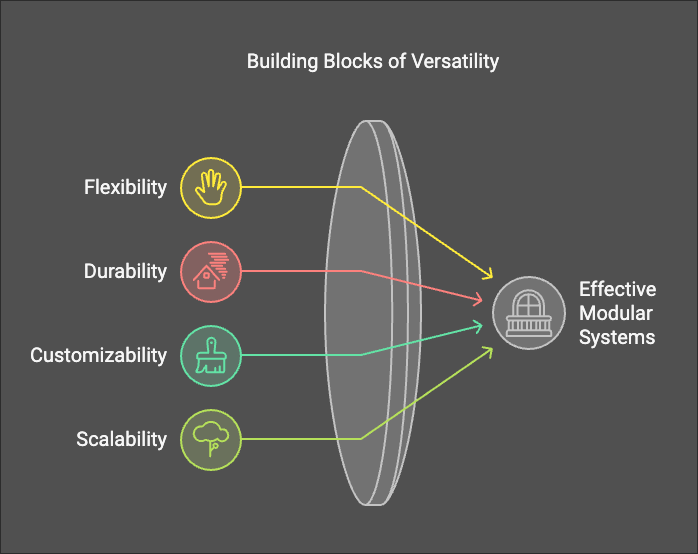
Enhancing Lean Manufacturing with Modular Systems
Modular systems boost lean manufacturing by offering flexibility, scalability, and efficiency. They simplify workflows, reduce waste, and adapt quickly to changing needs.
Eliminating Waste (Muda)
Lean manufacturing aims to eliminate the 7 types of waste (Muda), including overproduction, waiting, and motion inefficiencies.
How Modular Systems Help:
- Reduce Motion Waste: Tools and materials are stored closer to the point of use.
- Minimize Waiting Time: Quick assembly reduces delays in production setup.
- Limit Overproduction: Systems can be easily adjusted for just-in-time production.
Example:
A manufacturer reduces motion waste by implementing mobile trolleys and custom shelving using modular frames, cutting retrieval time by 20%.
Supporting Continuous Improvement (Kaizen)
Lean manufacturing emphasizes Kaizen, or continuous improvement. Modular systems are ideal for iterative changes.
Advantages:
- Easy to test and implement improvements without downtime.
- Allows teams to experiment with layouts for better efficiency.
- Facilitates quick scaling to meet demand fluctuations.
Example:
A packaging company optimizes its packing area by experimenting with modular setups, improving workflow by 15%.
Promoting Flexibility and Scalability
Market demands change, and production lines need to adapt quickly. Modular systems allow businesses to:
- Reconfigure layouts for new product lines.
- Scale production up or down without costly renovations.
- Enable rapid prototyping and adjustments for custom orders.
Real-World Example:
An automotive parts manufacturer uses modular workstations to adjust assembly lines, reducing lead time by 30% during seasonal demand spikes.
The Ergonomic Advantage: Employee Efficiency and Safety
Ergonomics is an integral part of lean manufacturing, ensuring employees are safe, comfortable, and productive.
How Modular Systems Enhance Ergonomics:
- Adjustable heights and designs to suit different workers.
- Improved accessibility to tools and materials.
- Reduced physical strain through optimized layouts.
Impact:
- 20% increase in worker productivity.
- Fewer workplace injuries, reducing downtime and compensation costs.
Cost-Effectiveness: Saving Time and Money
Investing in modular tube and joint systems is cost-effective in both the short and long term.
Key Financial Benefits:
- Lower Upfront Costs: No need for heavy machinery or permanent installations.
- Reduced Downtime: Quick assembly and adjustments keep production lines running.
- Scalable Investment: Systems grow with your business, reducing future infrastructure costs.
Case Study:
A warehouse facility reduced material handling costs by 25% by switching to modular racking systems.
People also read more about How to Find an Animator Job with Animyjob.
Sustainability: Lean and Green Solutions
Modern businesses are prioritizing sustainability, and modular systems align perfectly with green manufacturing goals.
Environmental Benefits:
- Made from recyclable materials, minimizing waste.
- Supports lean principles by reducing excess inventory and overproduction.
- Promotes reusability as systems can be repurposed for different tasks.
Example:
A logistics company repurposed modular racks for multiple projects, eliminating 15% of material waste.
Future Trends in Modular Systems
Smart Systems with IoT Integration
- Sensors track real-time inventory levels and system performance.
- Data analytics identify optimization opportunities for layouts and workflows.
Automation-Friendly Designs
- Modular systems are increasingly being adapted to integrate with automated assembly lines and robotic systems for improved efficiency.
Conclusion: A Foundation for Lean Manufacturing Success
Modular tube and joint systems are more than just structural frameworks—they are the backbone of lean manufacturing success. Their flexibility, scalability, and cost-effectiveness make them indispensable for businesses aiming to stay competitive in an ever-changing industrial landscape.
By eliminating waste, supporting continuous improvement, and promoting sustainability, modular systems align perfectly with lean principles.
Call-to-Action:
Ready to enhance your production efficiency and scalability? Complete Lean Tube offers customized modular solutions tailored to your needs.
👉 Visit Complete Lean Tube today and transform your manufacturing process for the future.